In the world of manufacturing, the lifespan and performance of machine blades are crucial for the productivity and profitability of any company. Dull or damaged blades can cause costly interruptions, slow down production, and decrease the quality of the final product. Therefore, keeping blades in optimal condition is essential to ensure efficient and profitable operation.
In this article, we will explore the best practices for maintaining industrial blades, how to identify when it’s necessary to sharpen or replace the blades. With this guide, we hope to provide companies with the necessary tools to optimize their cutting operations and maximize their productivity.
Proper Maintenance: The Key to Success
Proper maintenance of industrial blades is crucial for prolonging their lifespan and ensuring optimal performance. Here are the main aspects to consider:
1. Effective Cleaning
Effective cleaning is essential for maintaining the performance of industrial blades. Throughout the cutting process, it is common for residues, adhesives, and other contaminants to accumulate on the blades. These residues can negatively affect the sharpness of the blades and, consequently, the quality of the cut. To avoid this, it is essential to regularly clean the blades, removing any accumulated residue.
2. Routine Inspections
Regular inspections are a vital part of blade maintenance. Evaluating the blades regularly to detect signs of wear, damage, or misalignment can prevent major problems. By identifying these issues early, companies can take proactive measures to correct them, avoiding costly downtimes and ensuring that the blades operate efficiently.
Conducting routine inspections allows:
- Detecting cracks or microfractures in the blades.
- Assessing general wear and determining if the blades need sharpening or replacement.
- Verifying the correct alignment of the blades to ensure precise cuts.
3. Choosing the Right Materials
Selecting the appropriate material for the blades is crucial for their performance and durability. Blades should be made from materials suitable for the type of material being cut. Factors such as material hardness, sharpening angle, and type of coating also play a significant role in the performance of the blades.
4. Availability of Replacements
Having a good stock of sharp replacement blades is essential to avoid production stoppages. Replacement blades must meet the appropriate specifications to ensure they can be quickly replaced without compromising the quality of the cut.
Following these maintenance principles ensures that industrial blades remain in optimal condition, improving productivity and profitability.
Sharpening and Resharpening of Industrial Blades
Sharpening and resharpening blades are crucial maintenance aspects that should not be overlooked. With constant use, machine blades inevitably lose their edge, affecting operational efficiency and quality. Understanding the difference between these processes is important to apply proper maintenance:
Sharpening
Sharpening is the process of giving a blade a new edge when it is new or has been slightly used and has lost its initial sharpness. This operation is performed to keep the blade edge in its optimal shape. Sharpening can be done at any time when it is noticed that the blade has begun to lose its cutting ability, but before it is significantly worn.
Resharpening
Resharpening, on the other hand, refers to restoring the edge of a blade that has been used for a longer period and has suffered greater wear. This process involves not only sharpening the blade edge but also restoring its original shape, correcting any deformation or damage it has suffered over time. Resharpening may require removing a greater amount of material from the blade to correct these defects.
When to Sharpen
Knowing when to sharpen blades is essential for maintaining smooth operation. Several signs indicate it’s time to sharpen:
- Unusual Sounds and Vibrations: When cutting machinery starts to emit unusual sounds or vibrate irregularly, it is a common symptom that the blades are dull. These acoustic anomalies and vibrations occur because the blades cannot cut with the same precision and smoothness, causing greater machine effort and inefficient performance. In many cases, simply sharpening the blades can solve these issues, restoring the machinery to normal and efficient operation and eliminating annoying noises and vibrations.
- Blade Appearance: A detailed visual inspection of the blades can provide crucial clues about their condition. The presence of cracks, microfractures, or any other visible imperfections on the blade surface is a clear sign of wear. These signs not only affect the cutting capacity of the blades but also increase the risk of breaks during use. Machine parts such as bearings and hydraulic systems will suffer wear until they break.
- Reduced Performance: A clear sign that the blades are losing their edge is a noticeable decrease in machine performance. If work cycles are extended and the machine seems to struggle more to complete its tasks, it indicates that the blades are not cutting as efficiently as before. This increase in operation time not only slows down production but can also increase the wear of other machine components due to the additional effort.
- Jams During Operation: When blades start to lose their edge, one of the most common problems is machinery jams during operation. This problem not only slows down the production process but can also cause damage to the machine and the material being worked on. The underlying cause of these jams is the inability of dull blades to cut efficiently, leading to material accumulation and obstructions.
- Decreased Cut Quality: One of the clearest indicators that blades need sharpening is a reduction in cut quality. This deterioration can be evident to the naked eye, but in some cases, a more detailed inspection using microscopes or even evaluating the smoothness to the touch is required. Cuts that were once clean and precise can start to show rough or frayed edges. These signs are a clear indication that the blades have lost their edge and require immediate maintenance to restore optimal performance.
Sharpening and Resharpening Process
Sharpening and resharpening are procedures that must be performed precisely. To ensure optimal results, consider the following aspects:
- Quality Sharpening Equipment and Proper Techniques: Investing in high-quality sharpening equipment or hiring professional services can ensure precise and consistent sharpening. Professional services ensure that proper sharpening techniques are followed, and the specific angles recommended by the blade provider are maintained. This is crucial for optimally restoring the edge and maintaining blade performance.
- Sharpening Frequency: The frequency with which blades need sharpening depends on the type of material being cut and the intensity of use. Establishing a regular maintenance schedule can prevent excessive wear and prolong the blades’ lifespan. Adjusting the sharpening schedule to the specific needs of the operation can maximize the efficiency and durability of the blades.
Benefits
Sharpening and resharpening not only restore the blade’s edge but also offer significant advantages:
Prolongs Lifespan: Regular maintenance through resharpening can significantly extend the blades’ lifespan, avoiding premature replacements and ensuring sustained performance.
Improves Efficiency: Well-sharpened blades significantly improve machinery efficiency, reducing the effort needed to process and, consequently, improving the final product quality. This contributes to a smoother and less demanding operation for the equipment.
Reduces Costs: By prolonging the blades’ lifespan and optimizing operational efficiency, regular sharpening and resharpening can significantly reduce costs associated with frequent blade replacements and downtimes. Fewer production interruptions translate into greater savings and increased profitability.
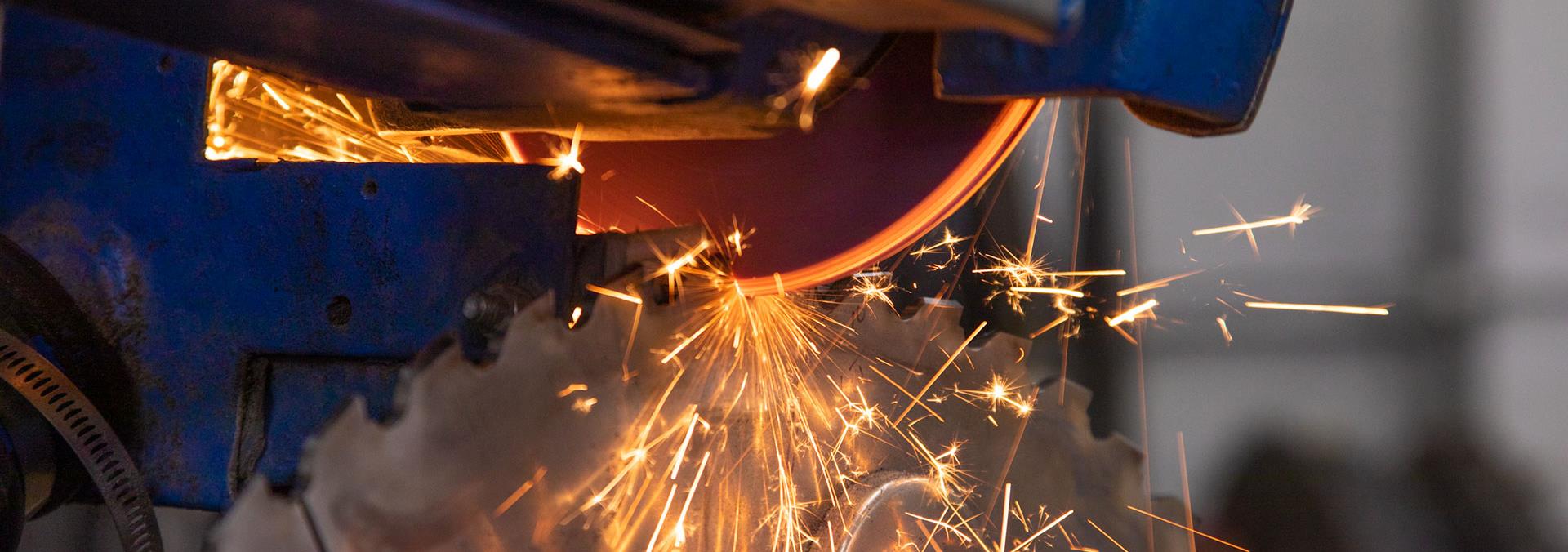
Maintaining a well-structured sharpening and resharpening program is essential to ensure that industrial blades operate at their maximum potential, thus optimizing productivity and profitability.
Blade Replacement: When to Say Goodbye
Knowing when to replace blades is as important as knowing when to sharpen them. Sometimes, the wear or damage is so significant that sharpening or resharpening is no longer sufficient to restore the blade’s performance. Here are the clear signs that it is time to replace the blades:
- Excessive Wear: If the blade shows considerable wear that affects its structure and performance, it is time to replace it. Continuous sharpening cannot compensate for the excessive loss of material and a significant decrease in cutting efficiency.
- Cracks or Fractures: Visible cracks or fractures in the blades are signs that they are no longer safe to use. Continuing to use damaged blades can result in catastrophic machinery failures and possible injuries.
- Deformation: If the blade has lost its original shape due to prolonged use or severe impact, it must be replaced. Deformations can compromise the precision and quality of the cut, as well as the integrity of the machine and the operator.
- Inadequate Performance Even After Sharpening: If, after several sharpening and resharpening cycles, the blade still does not perform as expected, it is a clear indication that it needs to be replaced.
Replacing blades on time ensures that the machinery operates efficiently and safely, avoiding major problems and ensuring the final product’s quality. Maintaining an adequate supply of new blades is essential to minimize production interruptions and keep a continuous workflow.
Do You Need to Sharpen Your Industrial Blades?
At Cuchillas Castillo, we offer a fast and efficient sharpening service across the peninsula, with a response time of just 72 hours. As manufacturers, we perform sharpening and resharpening with all guarantees to ensure the blades are like new, using proper cooling and achieving dimensional uniformity of all blades with exact sharpening, no more and no less than necessary.
The service includes the collection and delivery of the blades, facilitating the entire process for our clients. Thanks to our management system, we can provide the traceability of your blade sharpening, so that you can know the status of your blades, the available sharpenings, and the total cost throughout their useful life at any time.
We facilitate the sharpening of your blades in just 72 hours across the peninsula. Just call us at +34 961 255 380, and our logistics department will take care of the rest.